With the continuous development of science and technology in modern society, robot technology is playing an increasingly important role in industrial production. The use of coordinate systems is also crucial for precise positioning and manipulation of robots and arms.
In robotics, the coordinate system is used to describe the position, attitude and motion trajectory of each part of the robot.
The commonly used coordinate system and its application are very important to the operation of industrial robots, so it is necessary for us to have an understanding of these knowledge points, which is also of great help to operators or technicians.
1-The role of coordinate system in robot
A coordinate system is a mathematical concept used to determine the position of a point in space. In robotics, the coordinate system is used to describe the relative position, attitude (Angle) of each part of the robot body, and the working space of the robot. The coordinate system can help the robot to carry out accurate spatial positioning during the task, avoid collision, and ensure the accuracy of operation.
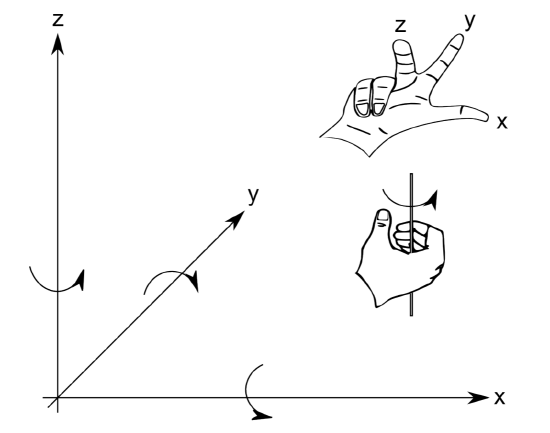
The robot coordinate system is usually composed of the origin, axis direction and unit, and can be defined according to different needs and tasks.
2-The robot commonly used coordinate system
In the field of industrial robots, the most commonly used coordinate systems include: base coordinate system, tool coordinate system, world coordinate system and joint coordinate system. Each coordinate system has its specific application scenario.
2.1 Base coordinate system
The base coordinate system is the “reference coordinate system” of the robot system, usually also called the world coordinate system or fixed coordinate system. The origin of the base coordinate system is usually set at the position of the robot base, and its axis matches the working space of the robot.
In robot control, the base coordinate system is used to describe the starting point of robot motion and the overall positioning. The path planning and motion control of robot all involve the use of base coordinate system. The base coordinate system is the most basic and important coordinate system in the industrial robot system, and all other coordinate system definitions are usually associated with the base coordinate system.
2.2 Tool coordinate system
The tool coordinate system refers to the coordinate system connected with the end effector of the robot (such as the grasping device of the robot arm, welding gun, spraying tool, etc.). The origin of this coordinate system is usually located at the operating point of the end-effector, and the direction of the axis is consistent with the actual direction of the tool.
The tool coordinate system is very important for accurately controlling the position and attitude of the robot’s end effector, especially when complex tasks (such as welding, assembly, spraying, etc.) need to be carried out, the robot uses the tool coordinate system for accurate operation.
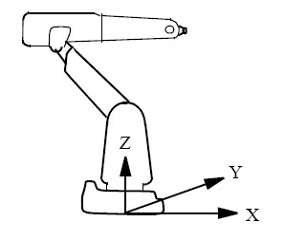
2.3 Joint coordinate system
The joint coordinate system is a coordinate system defined based on the motion of each joint of the robot. The coordinate system of each joint is defined on the axis of that joint, so the joint coordinate system is usually set according to the movement structure of the robot.
Joint coordinate system is suitable for describing the position and Angle of each joint of the robot, and is usually used for kinematics analysis of the robot. For many robotic arms, the joint coordinate system is the most direct control coordinate system, because the movement of each joint of the robotic arm is controlled according to the joint Angle.
2.4 World coordinate system
The world coordinate system is usually regarded as a fixed coordinate system, similar to the base coordinate system. It is used to describe the physical location in the robot workspace, and all task planning and path tracking are based on this coordinate system.
For some multi-degree-of-freedom robots or multi-machine cooperative systems, the world coordinate system is the basis of coordinating the movement of each robot or robot arm. In some complex automated production, the cooperation between robots is often through the world coordinate system to ensure the synchronization and accurate positioning of each other.
2.5 Workpiece coordinate system
The workpiece coordinate system is the coordinate system related to the target object operated by the robot. It is usually related to the position, orientation and state of the workpiece within the working area of the robot.
For example, when the robot performs tasks such as assembly or welding, the workpiece coordinate system can help the robot accurately position the workpiece, so as to complete accurate operations. The origin of the workpiece coordinate system is generally set in a specific position of the workpiece, and the coordinate axis is set along the length, width and height of the workpiece.
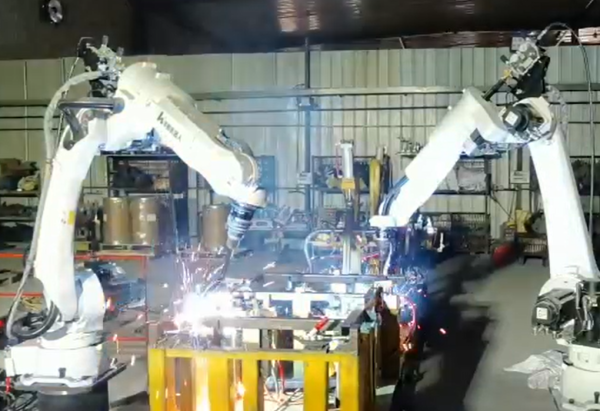
3-Transformation and application of robot coordinate system
When the robot is working, it often needs to convert the coordinates between different coordinate systems, which is called coordinate system conversion. Since robots often switch between multiple coordinate systems, coordinate system transformation is a very important part of robot control system. The transformation of coordinate system is not only a problem of mathematical operation, but also involves the kinematics and dynamics analysis of robot.
For example, when a robot performs a task, the position of the end-effector is controlled by the tool coordinate system, while the path planning of the robot is usually carried out in the base coordinate system or the world coordinate system. Therefore, the transformation of the coordinate system ensures that the robot can seamlessly switch between different coordinate systems to achieve accurate operation.
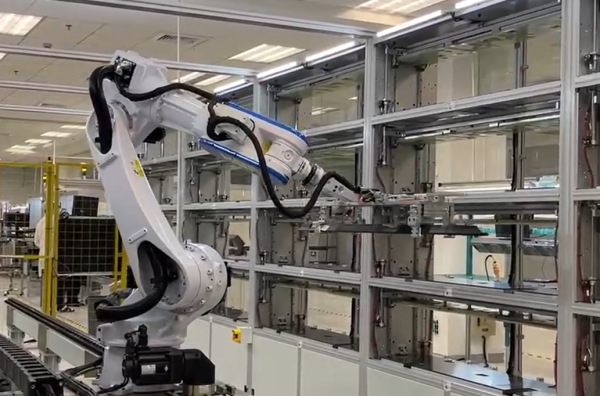
4-Coordinate system application in industrial robots
In industrial robots, the use of coordinate system runs through the entire robot workflow, including path planning, motion control, task execution, etc. Taking the welding robot as an example, during welding operations, the position of the end of the welding torch is usually controlled by the tool coordinate system, and the relative position and attitude of the workpiece are defined by the workpiece coordinate system. The robot needs to plan the overall motion trajectory according to the base coordinate system or the world coordinate system to ensure that the end effector is precisely aligned to the welding position.
In the assembly operation, the robot can control the motion of each joint through the joint coordinate system to complete the precise operation task. In some multi-robot cooperative systems, the robots work synchronously through a shared world coordinate system to ensure that each robot can operate according to a predetermined path and avoid conflicts.